Rapid Injection Molding: The Hidden Advantage for Fabricators
Within the current fast-paced manufacturing environment, the quest for effectiveness and swiftness has become paramount. Companies are constantly seeking methods to reduce lead times and enhance production methods, and one method that has emerged as a game-changer is rapid injection molding. This innovative technique is revolutionizing the way products are developed and introduced to consumers, enabling manufacturers to respond to consumer needs with unprecedented agility.
Rapid injection molding not only simplifies the production workflow but also significantly lowers costs associated with traditional manufacturing practices. By employing advanced techniques and resources, manufacturers can create top-notch prototypes and production parts in a much shorter duration. This ability to quickly modify and refine designs empowers businesses to stay competitive, adhere to tight deadlines, and deliver outstanding products to their customers. As the need for quicker and more effective manufacturing solutions continues to grow, rapid injection molding stands out as a valuable tool that manufacturers must consider.
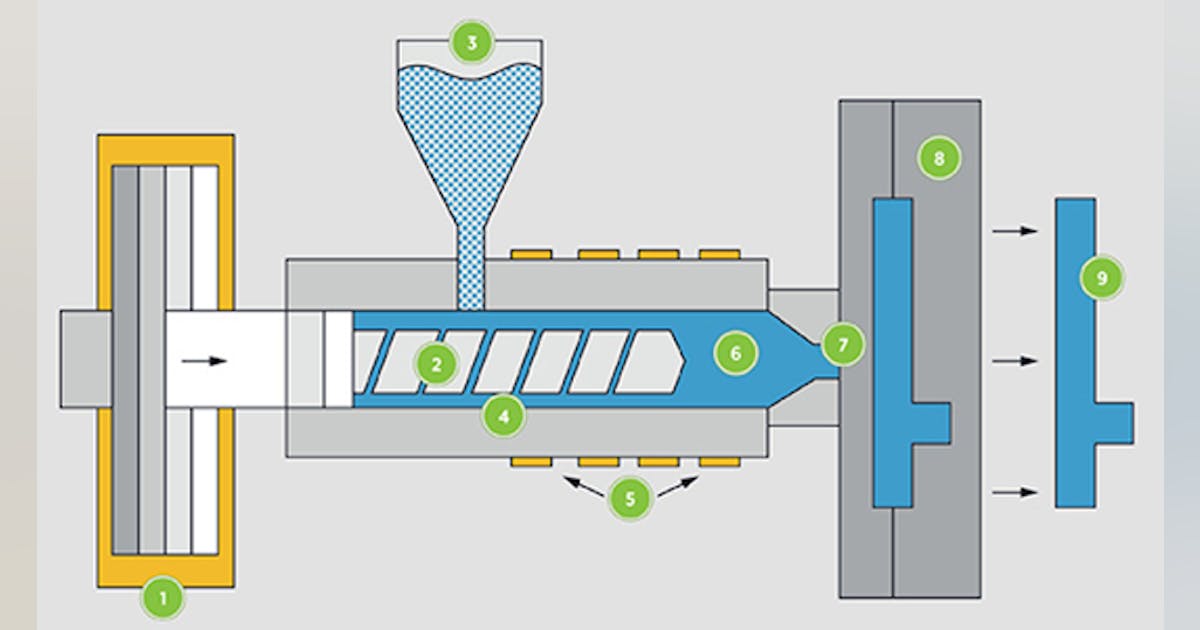
Benefits of Rapid Injection Molding
Rapid injection molding provides manufacturers a special mix of quickness and efficiency that differentiates it from traditional injection molding methods. One of the key advantages is the considerably reduced lead time for creating molds and parts. While traditional methods may need weeks or even months to have a mold set, rapid injection molding enhances this process, often completing it in a matter of days. This effectiveness allows companies to introduce products to market more quickly, giving them a leg up in fast-paced industries.
A further, advantage is the cost-effectiveness of rapid injection molding for limited production runs. Traditional molding can require high initial costs connected with mold creation, which renders it less feasible for smaller production quantities. In contrast, the rapid approach employs advanced technologies and materials that lower costs without compromising quality. This establishes it as an optimal solution for businesses looking to test products or customize items without significant upfront investment.
Lastly, rapid injection molding enables greater flexibility and design freedom. Companies can readily make adjustments to their designs because of the faster turnaround times associated with rapid processes. This flexibility allows for iterative testing and feedback, ultimately leading to improved product designs and greater customer satisfaction. With rapid injection molding, manufacturers can react to market needs swiftly, guaranteeing they stay relevant and in the game.
Applications in Multiple Industries
Rapid injection molding has shown to be an essential tool for multiple industries, greatly enhancing their fabrication processes. In the car sector, for example, manufacturers utilize quick injection molding to create complex parts and components in a small portion of the time it normally takes. This speed not only hastens the design cycle of innovative vehicles but also allows for rapid adjustments to designs based on consumer needs, ultimately leading to enhanced competitiveness.
The medical industry also profits substantially from rapid injection molding. With strict regulations and a constant need for precision, medical device manufacturers turn to this method for producing vital components such as housings and connectors. Rapid injection molding enables these manufacturers to produce prototypes swiftly, facilitating more rapid testing and compliance with safety standards, which is crucial in the life-saving field.
Moreover, the customer products sector has embraced quick injection molding to meet quickly shifting consumer preferences. Companies in this field can quickly produce limited quantities of tailored products or limited editions, reacting to consumer demands almost in real-time. This ability to innovate and bring products to market swiftly gives them a significant advantage over competitors who count on conventional manufacturing methods.
Future Trends and Innovations
In the realm of continue to find ways to improve efficiency and reduce costs, rapid injection molding is poised to transform considerably. New technologies such as artificial intelligence and AI are emerging to have a crucial role in enhancing the production and design workflows. These innovations can yield enhanced precision in mold design, live monitoring of production parameters, and faster adjustments to the manufacturing process. As a result, companies can look forward to briefer lead times and more efficient production cycles while ensuring high quality standards.
Another exciting development is the incorporation of eco-friendly practices within rapid injection molding. As recognition of environmental impacts increases, manufacturers are increasingly looking to embed biodegradable materials and recyclable materials into their supply chains. Developments in material science are resulting in a greater range of environmentally friendly polymers, allowing companies to satisfy consumer demands for sustainability without compromising functionality. This shift not only promotes environmental responsibility but also creates new markets for manufacturers embracing greener solutions.
Ultimately, the future of the field may also involve enhanced customization features. As the growth of on-demand manufacturing and the drive for customized solutions, businesses can utilize rapid injection molding to create custom solutions that address particular customer needs. This flexibility not only enhances customer satisfaction but also positions manufacturers as flexible players in a challenging market. As technology progresses, the potential for this process to change and innovate will be a significant driver of its success in the manufacturing landscape.